How to choose the type of zirconium ramming material for gla
In the construction of glass melting furnace, there are two kinds of zirconium ramming materials commonly used, namely zircon ramming and electrofusion AZS enamelling, although both zirconium ramming materials have good anti-glass. Liquid erosion performance, only very low pollution to the glass, but still need to be properly selected according to the nature of the glass produced.
So how does the glass melting furnace choose the type of zirconium ramming material?
The pores are the channels through which the glass liquid penetrates into the ramming material. The porosity is high, and the ramming material is resistant to chemical corrosion. This is because the pores are mostly concentrated in the bonding phase. Once the glass liquid penetrates into the ramming material, the gas phase, the glass phase and The etchant meets in multiple phases, forming a weak point against erosion. Therefore, if the chemical composition is constant, the lower the total porosity, the stronger the erosion resistance.
The type and composition of the etchant also plays a large role in the erosion resistance of the ramming material. In glass kiln, the etchant mainly refers to the high temperature glass liquid and the dense metal or metal oxide deposited on the bottom of the pool. Different glass solutions have different effects on the ramming material. The characteristic rate of erosion and the form of erosion are very different between soda-lime-silica glass, borosilicate glass, lead glass and other types of glass.
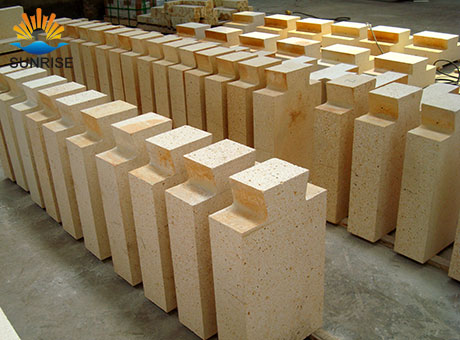
The main difference between fused AZS ramming and zircon ramming is the content of Al2O3 and porosity. Since there is a masonry gap in the paving brick located on the upper layer of the zirconium ramming material, the glass liquid will penetrate into the ramming layer through the brick joint, and the erosion resistance of the ramming material will be due to the chemical composition, moving speed and temperature of the glass liquid. Different. The soda-lime-silica glass melt is highly aggressive due to the ionized alkali in the melt, and the ionized alkali is the driving force of the corrosion mechanism when they are in contact with the ramming material.
The viscosity of the melt also has a large effect on the rate of erosion, regardless of which glass system is in the range, and the erosion increases sharply with decreasing viscosity.
Pre:
Teach you a Few Tips for Choosing Quality Refractory Materia
Next:
Explain the scope of application of refractory insulation br